Collin Jones
Architectural Engineering
Lighting/Electrical​
BUILDING STATISTICS
General Information
Project Team
Building Name | Conewago Enterprises Office Facility
Location | Hanover, Pennsylvania
Building Type | Office
Construction Classification | Type III
Occupancy Classification | Business - B
Size | 33,000 sq. ft.
Number of Stories | 3
Building Height | 51'-7"
Owner/General Contractor | Conewago Enterprises, Inc.
MEP Engineers | Paragon Engineering Services, Inc.
Architect | Jim Baumgardner
Structural Engineers | Conewago Enterprises, Inc.
Rendering Courtesy: Jim Baumgardner
Architecture
Conewago Enterprises office facility is a 3-story building that is used for their general contracting business. The lobby façade comprises of stone veneer on pre-cast concrete sandwich panels and an aluminum curtain wall system. The rest of the building utilizes a pre-cast concrete sandwich panel system with aluminum coping system. The interior of the space is a rectangular form which provides spaces for private and open offices, a two-story lobby, conference rooms, a training room and spaces to expand in the future on the upper level.
Codes
-
International Building Code, 2006
-
International Existing Building Code, 2006
-
International Energy Conservation Code, 2006
-
ICC Electrical Code, 2006
-
International Fire Code, 2006
-
International Mechanical Code, 2006
-
National Standard Plumbing Code, 2006
Building Enclosure
Wall Facades
There are 3 major facade systems utilized on this building:
​
Type A1 | 9" insulated wet-cast concrete paneling with stone veneer on the exterior side of the building. This type is located on the front of the lobby.
​
Type B1 | 9" insulated wet-cast concrete paneling. This is the primary facade used on all 3 floors for most of the building.
​
Type C1 | Exterior side consists of 9" insulated wet-cast concrete paneling. Interior side of the wall comprises of metal studs spaced 16" on-center, R-13 fiberglass insulation, metal channel stiffeners spaced 5 feet on-center, and 1/2" gypsum wall board. Type C1 is located on the northeast corner of the building on the main floor and serves private office and conference room spaces.
​
​

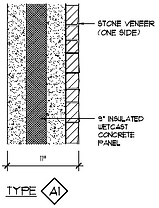


Window/Curtain Wall
The main lobby features a 2-story curtain wall façade and the office areas are commercial fixed windows with a pre-finished aluminum framing. The exterior glazing is 1” insulated heat strengthened PPG SOLARCOOL® reflective with SUNGATE® 500 low-emissivity glass throughout the building. The interior glass for the fixed windows is ¼” heat strengthened clear glass with internal blinds.
Roofing
The roofing system consists of a fully adhered thermoplastic polyolefin (T.P.O.) roofing system throughout with a 5” polyisocyanurate insulation and a pre-finished aluminum coping system. A portion of the roof is dedicated to a green roof discussed in further detail in the following section.
Sustainability Features
Green Roof
A portion of the roof is dedicated for green roof space. On top of the roofing system is a gravel fill area, green roof planting, and a patio space that includes a small seating area. Pavers and walkway pads allow easy service to the roof top units and pumps located on the roof.

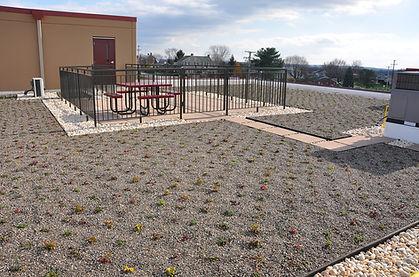
Green Roof
Photo Courtesy: Paragon Engineering Services, Inc.
Shading
The front elevation of the building faces in the south direction, which is problematic for direct sun penetrating into work spaces. Direct sun causes problems involving glare to increase. A combination of individual and continuous runs of exterior horizontal sunshades on the south, east, and west facades. This element dually functions as an aesthetic element to the building. Exterior overhangs function to control direct sunlight from getting into the lobby space.
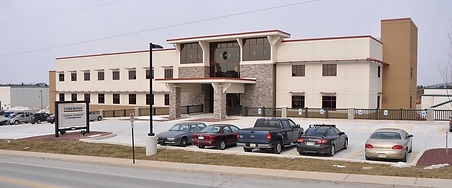
Front Exterior Horizontal Shading
Photo Courtesy: Paragon Engineering Services, Inc.
The lighting design of the facility primarily consists of fluorescent, metal halide, and halogen lamps. The office areas feature a mixture of suspended and recessed linear fluorescent fixtures dependent upon the ceiling layout and application. Recessed downlights are provided in conference rooms, the training room, and lobby. Decorative glass pendant fixtures with metal halide lamps provide ambient lighting for the open lobby space. This area also uses halogen track lighting to highlight features on display near the main entrance. The exterior consists of metal halide flood lighting and in-grade fixtures for the front entrance and exterior wall mounted fixtures for the parking lot behind the building.
Lighting Controls
An eight-relay lighting panel controls the lighting in some areas of the building. The first six relays control the corridors and general lobby lighting. These areas are time controlled and turn on at 8:00am time and shut off at 5:00pm. All spaces feature an override switch with a 15-minute time delay. Relay 7 controls pendant fixtures at the front of the lobby and provide illumination of the curtain wall system. These lights are turned on at dusk by a photocell and an astronomical time clock shuts off the fixtures at 11:00pm. Relay 8 controls all exterior and parking lot lighting and has an astronomical time clock for the on and off times. The panel is flexible and allows times to be adjusted as necessary. All other spaces including open and private offices, conference rooms, and restrooms are controlled by power pack relays with occupancy sensors. The use of time control and sensors increase the energy efficiency for the building by automatically extinguishing lighting when and where it is not needed.
Building Systems
Lighting
Electrical
Metropolitan Edison (Met-Ed) provides electricity to multiple existing buildings on the site, the electrical service goes to a power company pad mounted transformer to step the voltage down to 480/277V – 3 phase power. The conductors then enter a CT/Metering Cabinet and an 800A transfer switch. The transfer switch, located in the existing weld shop on the site, feeds a wire trough with multiple existing switches and electrical panels. A 600-amp feeder provides power to a main distribution panelboard located in the office building. The main distribution panel then feeds three 480/277V panelboards that serves the rooftop units and lighting equipment. Each of these panelboards then feed a transformer to step down the voltage to 120/208V panels for receptacle and other power circuits.
A 600-kilowatt diesel powered generator on site provides emergency and standby power the entire building. A 30 amp, 3-pole circuit breaker located on the generator feeds one automatic transfer switch for the emergency lighting panel and exterior lights. Another 800 amp, 3-pole circuit breaker feeds the previously mentioned 800-amp automatic transfer switch and provides standby power to all of the buildings located on the site.
​Different systems serve a variety of purposes that provide heating, cooling, and ventilation to the building. Split system heat pumps and air handlers work in conjunction to provide heating and cooling for the lower and main levels of the building. Each floor also contains an energy recovery ventilator that mixes return air with outside air in order to recirculate throughout the various split systems, thus reducing energy consumption. Five rooftop units on the upper level are provided for future expansion of the building. A sixth rooftop unit, coupled with a small energy recovery ventilator provides heating and cooling to the training room and restrooms on the upper level. Radiant heat tubing is built into the concrete floor systems and circulates hot water through a piping system with various zones. This provides another method of heating different spaces in the building.
Mechanical
The foundation of the building consists of 3000psi concrete with a 4” thickness. The concrete is reinforced using welded wire fabric with a vapor barrier and dow board insulation. Wall footings range from 2’-0” to 5’-3” in width and 15” to 24” in depth depending on the location. The first and second floors consist of 10” planks with 4” of concrete topping. On the left side of the building, planks frame into W24x62 girders. The right side of the building is framed with W24x117 girders. Type HSS columns of various sizes support the floor and roofing systems. The typical roofing system comprises of joist girders and 22 gauge type B metal decking. The green roof area utilizes 20 gauge metal decking to provide support for the additional dead load. The lobby space utilizes custom architectural joist girders and a 1-1/2” wood decking for the structural roof system.
Structural
The delivery method for the building was design-build. An existing office was demolished on the same site in order to construct a new building. Conewago Enterprises, Inc. was the general contractor for the project. The overall project cost was $3.7million and obtained LEED accreditation.
Construction
Office buildings heavily rely on telecommunication and data systems for their business to operate efficiently. Voice/data patch panels and racks are located in a server room on the lower level. A cable tray is routed through the center portion of the building. CAT 6 and CAT 5e cables are specified for use of data and voice, respectively. Cables are then ran to each voice/data jack throughout the building. A dedicated jack, located in a closet space, on each side of the building provides communication to a wireless access point, which gives authorized users in the building access to a wireless network.
Telecommunications
Specialized Systems
A fire alarm control panel, located in the lower level electrical room, provides automatic detection of smoke and fire within the facility. A fire alarm annunciator and manual pull station are located by the main entrance. Area of rescue assistance devices are located in both stairwells of the building to allow communication between a building occupant and personnel at the main annunciator located in the lobby.
Fire Protection
Transportation
One elevator in the office facility serves all three floors of the building. The main distribution panel for the building provides 480-volt, 3-phase power to the elevator controls and the 40-horsepower motor.